5 reasons why your organization's behavior-based safety process could soon collapse | FIRST, VERIFY
According to EHS Today typically 70 percent of safety-based initiatives undertaken by companies fail, resulting in the loss of money and productive man-hours. But what is a lot worse than the financial loss is the increased lack of confidence of both management and employees that follows – most frustratingly expressed as, "Our company is incapable of change."
Fortunately, today's companies, both national and international, have realized that antecedent and results-only safety programs cannot maximize safe performance. Safety processes that target the root cause of most accidents and incidents- human behavior, once ignored or rarely heard of, have now claimed the spotlight.
The new acceptance and implementation of behavior-based safety methods is a step in the right direction, but a few common missteps can prematurely cripple your organization's process.
The five biggest mistakes your company might make while implementing behavior-based safety are more on the lines of how and what they are trying to get people to do.
1. Believing that employee participation and observation are the core of behavior-based safety
The biggest risk a company's management can take is to assume that the organization has correctly implemented behavioral safety because the right observations are being performed by employees.
Behavior-based safety is about integrating behavioral technology into the management of safety in your company. Behavioral technology is the system and process for applying the laws and principles that govern human behavior. The objective of applying them is to achieve behavior change. Performing observations and allowing hourly employees to conduct those observations does not necessarily lead to changes in the way people behave at work. In most instances, it only changes the way they behave when they are being observed.
The primary objective of an effective behavior-based safety process is to make safe behavior a habit. Unsafe or risky behavior is usually habit-based. Most people aren’t conscious of their behavior having done things the same way much of their lives. The primary goal of behavior-based safety is to replace all the unconscious unsafe behavior with the unconscious, or automatic, safe behavior -- or safe habits.
To accomplish this objective, hourly employees, supervisors, and managers must understand and apply behavior change technology effectively.
2. Systematic positive reinforcement is key
As mentioned above changing organizational culture is not possible without a sufficient grounding in the basic principles of behavior. This deficiency is crucial when it comes to the culture of positive reinforcement.
Positive reinforcement is the key to substituting unsafe work habits with safe ones. If provisions have not been made in your safety initiative for training in the principles and application of positive reinforcement, then the natural reinforcement that is currently supporting unsafe work habits will continue to elicit that behavior.
In most cases, unsafe behavior or risk-taking happens because it has some natural positive reinforcers. For instance, a prankster gets away with his ‘funny’ pranks risking the safety of his fellow workers in most cases. Like hiding the ladder when his teammate is about to get down, or ‘accidentally spilling water so that someone can fall, etc. His whole life he must have received constant adulation and garnered the title of the ‘funny’ guy. And as such, this unsafe, risky behavior continues, out of a bad habit.
Risk-taking saves time, effort and sometimes can be seen as a shorter and quicker route to success. Unsafe behavior then is self-perpetuating because of the natural consequences that favor it.
With that concept in mind, it then follows that delivering regular positive reinforcement for safe behaviors is the key to replacing unsafe habits with safe habits. Managers, supervisors, and coworkers must deliver this reinforcement immediately, consistently, and appropriately or the safe behavior we are encouraging will never reach habit strength.
3. Expecting a change in only Temp employees
It needs to be understood that for a long-lasting change, every employee must make a behavioral change -- not just the temps. Management is integral to change, yet most initiatives target employee behavior alone.
Any behavior-based process should include mandatory support behaviors from both management and supervisors. This constitutes a measured self-inventory in the form of a checklist with points. A quantitative measurement feedback system helps form the basis of positively reinforcing managers and supervisors for specific behaviors related to supporting the behavior-based safety process.
This in turn helps temp employees increase the rate of safe behavior, while managers and supervisors are reinforced for their supportive behaviors.
4. Making behavior-based safety the responsibility of only the employees
Much too often, behavior-based processes are positioned and implemented as only employee-focused programs. This brings about the short-term, temporary changes visible in the form of specific bureaucratic activities which only focus on implementing change. Long term, however, these kinds of rules result in resentment in the employees related to the perception that are the only ones putting in all the effort to make the process work.
The side effect of such implementation of processes is that they die a slow death because employees get fed up with the additional work and responsibility without receiving the required positive recognition and reinforcement for their efforts.
5. Force fitting an itemized action plan to your organization
This mistake is accelerated by the belief that behavior-based safety is a sequence of actions, meetings, observations, and reviews, rather than a process that helps to change core safety behavior.
Most organizations assume that training, thorough paperwork, continued employee observations, and safety-related review meetings can ensure behavior-based safety. This cannot be guaranteed as monitoring or guiding a group of overworked, tired individuals can only lead to a loss in production, overtime, and time-off surge, and an absolute lack of motivation.
In contrast, implementing the basic principles and concepts of behavior-based safety processes provides you with an understanding of the rationales behind the activities and allows you to use your knowledge of behavioral technology to tailor and design a process that fits your requirements.
For example, an ideal behavior-based training should include the following elements:
- Employee action should not be observed for more than five minutes.
- Observe only two or three behaviors at a time.
- Integrate observations into the work process so that there is no time off the job.
- Design self-observations for employees who operate vehicles or work alone.
Many of the programs now implemented do not use the practices listed above. Those familiar with behavior technology know that the shorter list is not only more desirable but is impactful and quicker.
The five reasons or risks in successfully implementing a behavior-based process are centered around a core misunderstanding of what a behavior-based safety process is. The correct approach begins with an in-depth knowledge of how to change human behavior.
A well-designed and properly implemented program can be effective and is a great workplace safety solution. It not only positively impacts a company’s profits and reputation, but it also has a profound impact on the lives of employees as poor decisions or unsafe behaviors can lead to loss of livelihood or even fatalities.
You might also like
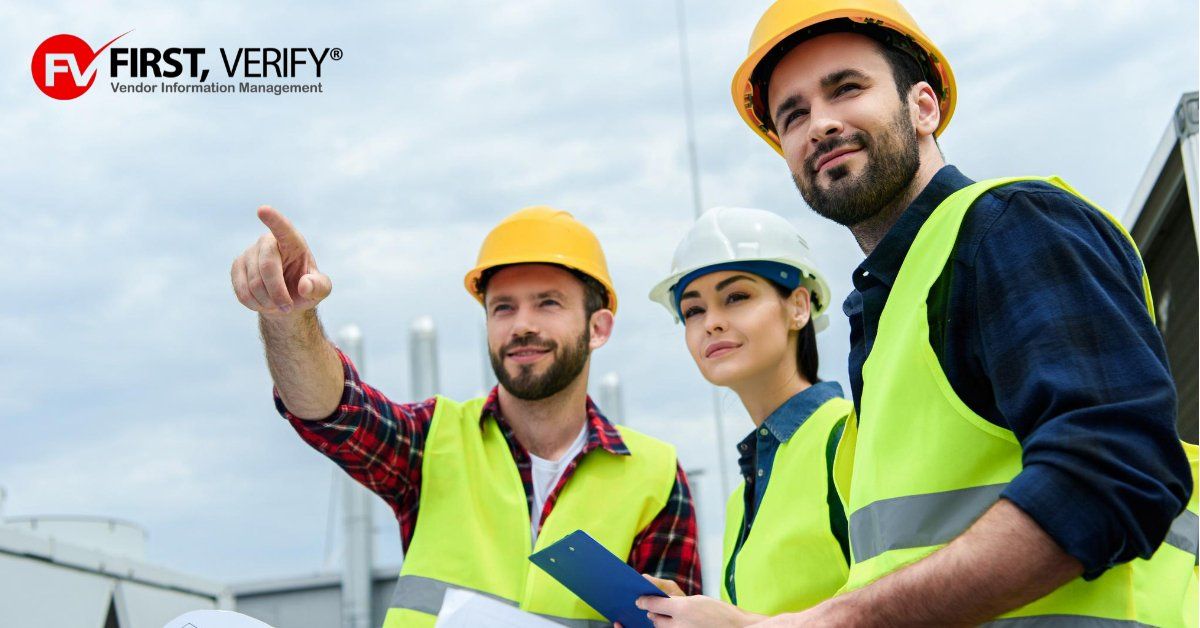