Do You Believe in Safety?
Elaine Taylor recalls back in the mid 1990s when one of her employees – a young carpenter – was wrapping up work at the end of the day replacing the roof on a fire-damaged home. It was winter time in Alaska, and the crew had just finished spreading plastic sheets to cover the roof openings. One feature of plastic is its low co-efficient of friction, especially when icy and laying at a 23° angle. One feature of young carpenters is an attitude of haste, another is of invincibility. Unfortunately, he lost his footing and in less than two seconds, he had fallen 21/2 stories – over 30 feet – hitting the frozen ground at around 32 mph without wearing any fall protection equipment.
Fortunately his landing was cushioned by snow, otherwise he might have died. Nonetheless, he broke his lower back and never again returned to work as a carpenter. He was off of work for a year and had to get training to work in another industry. “It changed his life forever,” Taylor said wistfully.
The companyTaylor owns with her husband Larry and their childrenTrent and Lisa –Taylored Restoration, in Anchorage – had been technically compliant with AKOSH regulations. They had their safety meetings, they had a safety program, but they didn’t follow up in a systematic fashion to ensure that employees were implementing the procedures. “We talked the talk, but didn’t walk the walk,”Taylor says. “It wasn’t really key to our beliefs.”
Before the accident, AKOSH would inspect their commercial work, but after the accident they became a larger dot on AKOSH’s radar. It didn’t help when they filed the accident report late (the federal OSHA standard is less strict, requiring notification at three hospitalizations). The job site was a long way from the hospital, and they arrived so late they decided to wait until the next day to file, not realizing that their delay placed them in violation of AKOSH’s 24-hr. notice rule. That highlighted the need for better education in the
applicable OSHA regulations.
Fortunately, they didn’t incur any legal liability, but they paid a fine to AKOSH, and, of course, their EMR went up causing their worker’s compensation premiums to increase significantly. While the economic consequences were meaningful, the greater impact on the Taylors was the sobering human cost paid by their carpenter. At a subsequent meeting of the company leadership team, Taylor interrupted the discussion and declared, “We’re approaching this the wrong way. We need to look at safety as the first thing we think about. ”That initiated a fundamental change in the company’s operating procedures and culture.
Now, every employee has the authority to stop any activity they think is unsafe. If a worker has an accident, it’s addressed at the next company meeting and the employees discuss how it could have been avoided. Their safety policy is enforced rigorously in the field, resulting in actually firing some employees who had refused to comply and tie off. The company also works closely with their worker’s compensation carrier to ensure that their safety program is up to date.
Their subcontractors have to walk the line right along with them. On one project, an employee stopped other employees working for a subcontractor and kicked them off the job. On another project at an apartment complex, an employee spoke up during a job site meeting and insisted that a sub working for the apartment manager be tied off or Taylored would stop work. The apartment manager agreed and required the worker to wear his fall protection equipment. When a sub actually did fall off the roof, when he reached the limit of the line he swung back under the eave and into a tempered glass window. The impact left an imprint of his body on the glass, most likely damaging his pride but not his health.
Every new Taylored Restoration employee must now go through a formal safety orientation and is not allowed on a job until after watching a few key videos.There’s a company safety committee with oversight responsibility for the various departments—cleaning, office staff, large jobs, small jobs and so on.They are charged with continuous revisions to the safety manual and MSDSs, and with keeping employees’ safety awareness at top of mind. Safety presentations are run by different departments in rotation at the company wide monthly meetings. Creativity is encouraged, if not required—departmental employees produce skits, videos, and exercises to convey their lessons in new and memorable ways. One exercise pits workers in a relay race to help get them more familiar with tying off their fall protection equipment.
There’s no central database for residential construction, like Dodge Reports, from which OSHA can develop programmed inspection lists, leaving it to the off chance of a drive-by to initiate any scrutiny.This means that compliance in restoration isn’t driven by being closely watched, but instead by company culture. So if a contractor’s owners don’t have a genuine commitment to safety, the risk of serious injury or death can be too high.
You might also like
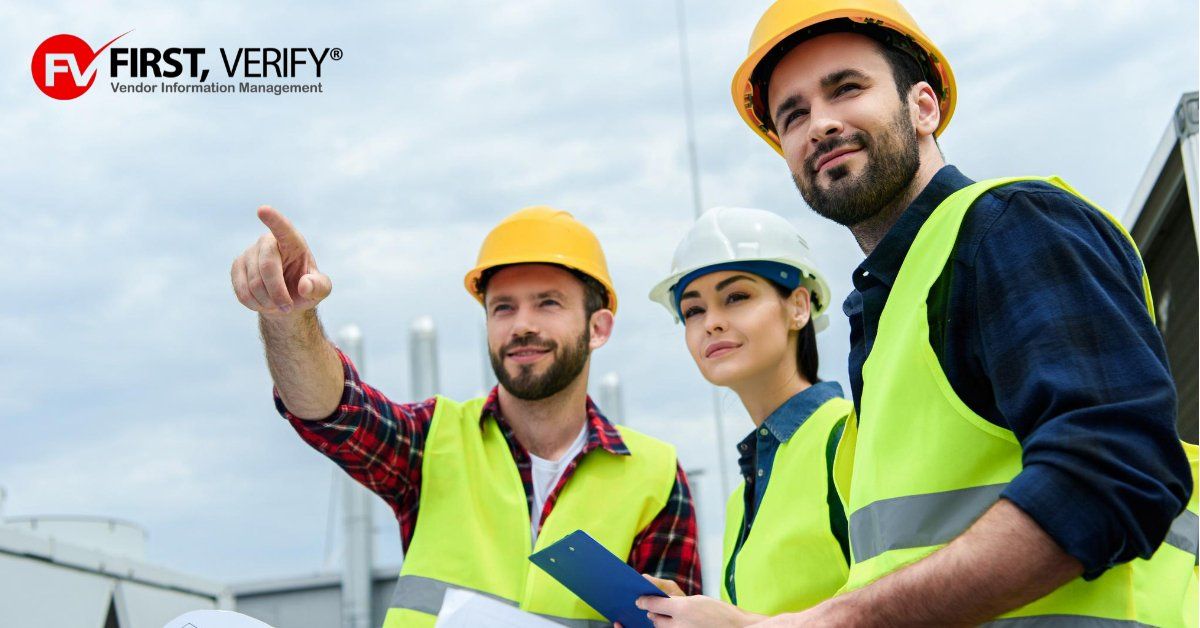