Measuring the effectiveness of safety training -Safety Orientation | FIRST, VERIFY
Most organizations have solid training programs in place, with class room and refresher courses conducted throughout the year for new and existing employees. However, despite the presence of comprehensive safety training, there is a risk that it becomes a “check the box” exercise.
OSHA recently announced that it will no longer rely on past employer safety data, or lagging indicators, it will now focus its efforts on leading indicators.
Leading indicators are defined as proactive, preventive, and predictive measures that provide information about the effective performance of your safety and health activities. They measure events leading up to injuries, illnesses and other incidents and reveal potential problems with your safety and health program. By comparison, lagging indicators measure the occurrence and frequency of events that occurred in the past, such as the number or rate of injuries, illnesses, and fatalities.
Leading Indicators
Participation in safety training is a popular leading indicator. In a National Safety Survey conducted in 2019, participation was tracked by 80% of the respondents, coming in third behind “Near-misses” (84%) and “Employee audits/observations” (81%). Typical metrics include:
- Total number of training hours provided
- Number of training hours provided per employee
- Percentage of training courses completed
- Percentage of new hires who completed safety orientation
In addition to tracking the above, you should also track leading indicators that measure the effectiveness of the training, to get a more accurate evaluation. Here are two examples of metrics:
- Percentage of improvement on post-training assessment scores over pre-training assessment scores (from OSHA’s document “Using Leading Indicators to Improve Safety and Health Outcomes”)
- Number and percentage of positive post-training evaluations for safety training (from the Campbell Institute’s Implementation Guide to Leading Indicators)
An easier way to implement measures would be to quiz participants to test their comprehension. The quizzes could be given immediately after a training session, but also later to see if they retained the knowledge (a month or two later).
Also, conduct post-training surveys to determine if workers had a positive or negative impression of the training. Include open-ended questions where employees can offer feedback and ideas for improvement.
Finally, as with all leading indicators set goals (and periodically reassess them) for the leading indicators used to measure the effectiveness of safety training. Don’t just track something for the sake of tracking it. Constantly monitor to determine if your goals are being achieved and take action if you’re not meeting them.
OSHA reinforces the fact that applying leading indicators can improve organizational performance in a variety of ways. By doing so, the agency says employers may find they can prevent workplace injuries and illnesses, reduce costs associated with incidents, improve productivity and overall organizational performance, optimize safety and health performance, and increase worker participation.
The benefits? The cost of injury prevention is less than one serious injury, and a safe and healthy workplace attracts and retains quality employees.
You might also like
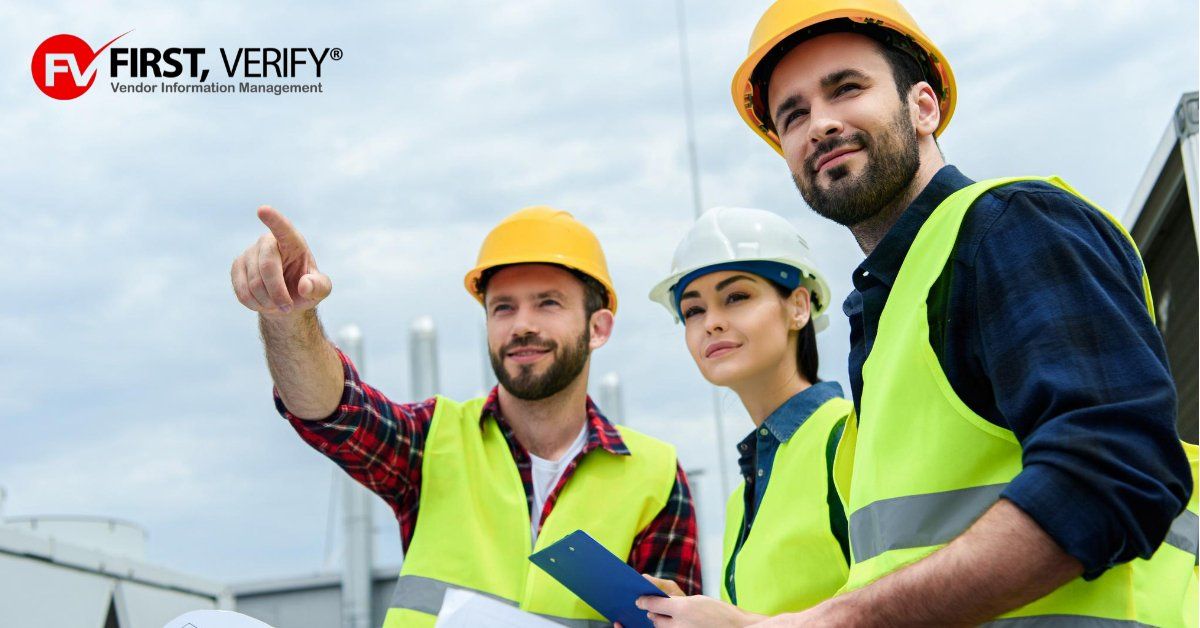