What You See is Not What You Get
Joel Dagenais knows how to build businesses. He began his career in the restoration industry in 1989 by doing it all for a small insurance restoration firm in Ottawa, Ontario – marketing, estimating and project management – helping to double the company’s volume during his three-year tenure. In 1992, he and a partner purchased a First General Services franchise. Having developed plenty of contacts in the insurance industry from the prior company, he was able to secure an exclusive relationship with a large insurer within two months. Selling his ownership interest to his partner that same year, he opened a First General Services office in Hull, Quebec, and grew that to the largest restoration contractor in the area.
While developing the Hull office he exercised an option to develop the entire province of Quebec, and sold 15 franchises for a total of 16 locations; and then in 2007 he sold the entire master franchise system. Along the way he also became the exclusive distributor for Xactware in Canada and in four years increased sales eight-fold. Early this year Dagenais acquired the franchisor company for the First General Services system in the U.S., based in Orlando, Fla.; and he hopes to expand the existing network throughout the U.S. within five years.
Having such a broad base of experience in the restoration industry means there are quite a few stories to share.One recollection involved a safety-related teaching moment: In the late ‘90s his company was working on a large commercial water loss at a private school. The workers were thoroughly trained in how to handle water mitigation. Back then they wore ordinary work clothes with some personal protective equipment such as respirators when needed. Their typical water loss jobs were residential where the worst risk was that some wet drywall might fall on someone; but the school was a commercial-style building. Among other typical commercial features, it had suspended ceilings with fibrous tiles and 2′ x 4′ fluorescent light fixtures covered by acrylic lenses.
Because it was a fair-sized loss, the project manager had gone to the site to make sure they wouldn’t miss any areas that needed drying or that might create mold issues.The crew was working on the second floor where the water damage had occurred, while the project manager was on the ground floor performing his inspection. Unbeknownst to the crew or the project manager, water had accumulated on the first floor’s ceiling tiles; in fact, the tiles had absorbed a tremendous amount of water, yet they had stayed intact rather than collapsing out of the grid.
The school was an older wooden structure and the crew’s work activity caused the second-floor joists to deflect. The ceiling grid was attached to those floor joists; and this movement, along with the accumulated weight of the now-sodden tiles, caused some of the fasteners to suddenly pull loose from the joists. The abrupt, partial drop twisted the steel grid; and because the light fixtures were just sitting in the grid rather than being independently attached to the joists, they dropped with the grid – causing several of the acrylic lenses to fracture into pieces that fell on the projec tmanager. Because he wasn’t wearing a hardhat, he suffered a deep gash in his head – about three to four inches long in a half-moon shape. Bad enough, of course, but he was fortunate not to have suffered a more serious injury. Had a larger and heavier object fallen on him, the consequences could have been fatal.
Dagenais is frank in acknowledging that they didn’t handle the safety precautions correctly. They never imagined that so much water could accumulate in a dropped ceiling without causing the individual tiles to cave in, but they still should have prodded the tiles to make sure there wasn’t a potential hazard. And they didn’t anticipate that the fasteners used to attach the grid to the second-deck joists might be inadequate for the added load caused by the accumulation of water.
Current commercial code would require that both the grid and the light fixtures be attached to the joists with screws – but because this was an older building they had been nailed, and the light fixtures were simply nested in the grid instead of being independently attached. One lesson learned was to never assume how a structure has been put together, even a commercial building.They treated what was in effect a construction site (which automatically would have warranted the wearing of hardhats) as an ordinary water mitigation job. Lesson two was to never repeat that mistake.
A commercial loss environment is very different froma residential loss environment. Even if a water mitigation crew is well-trained, they don’t necessarily know what’s behind the walls unless they’ve also been trained as general contractors. Unlike a fire loss, where potential hazards are well understood, the prevailing attitude with water loss work is, “it’s water… can’t hurtcha.” But experience is the best teacher, and Dagenais believes that it takes a licensed, fullservice general contractor – one that understands how a commercial building is constructed – to safely handle commercial restoration work.
You might also like
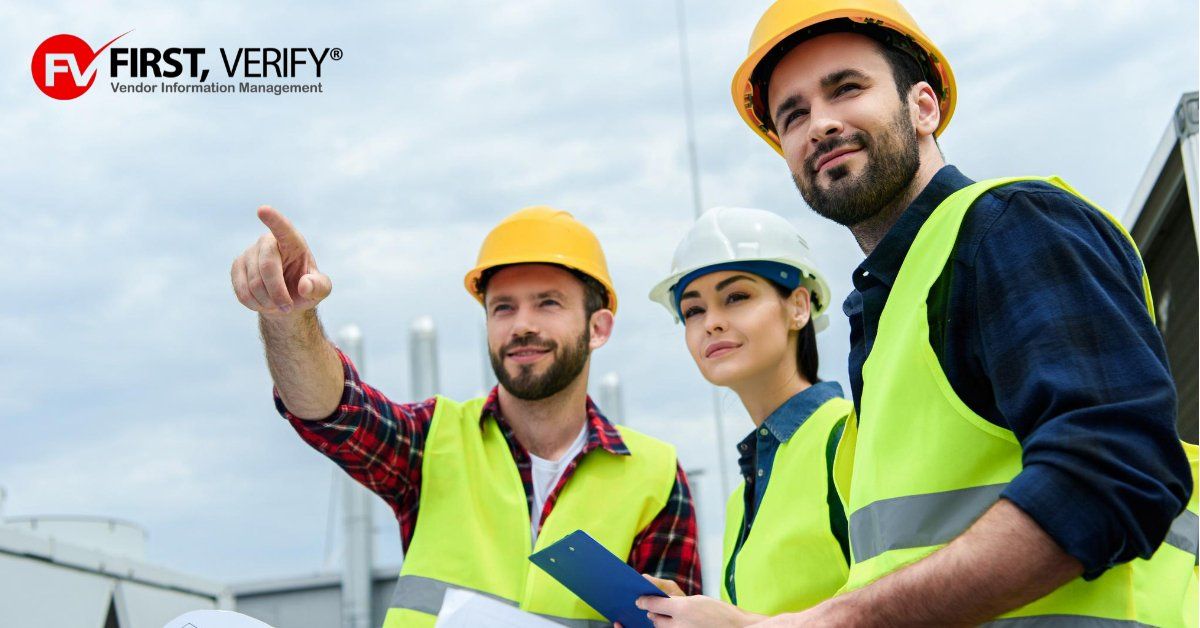