During an OSHA inspection: Know your rights
During an Occupational Safety and Health Administration (OSHA) inspection, the OSHA official, escorted by management, will tour the facility or construction site to observe working conditions, identify violations, and so on. However, an OSHA official cannot require equipment to be positioned a certain way or an accident scene be reenacted for photographs of an allegedly violative condition.
Knowing this, a company can save time and money. In Secretary of Labor v. North American Crane & Rigging LLC (NACR), OSHRC No. 20-1089 (Aug. 6, 2021), the employer successfully contested an OSHA citation based on two instances of failing to adequately mark hazardous area boundaries in violation of the crane standard at 29 C.F.R. § 1926.1424(a)(2)(ii). The judge agreed that no employees were exposed to the swing radius of two cranes.
Background
In this case, an OSHA Compliance Safety and Health Officer (CSHO) was driving by a construction site and saw a crane in use. He pulls over to start an inspection. One crane (yellow crane) was in the process of being used to disassemble another (red crane). While onsite, the CSHO observed the red crane’s superstructure rotating while two employees stand within feet of it. There were no barriers or warning signs because the red crane’s counterweights had been removed and its swing radius did not extend beyond the vehicle’s body. During the walk-around inspection, the CSHO was not observed to have taken any measurements of the red crane. The CSHO observed the yellow crane’s superstructure rotate with its attached counterweights extending several feet past the extended outriggers. Through pre-planning, all lifting and landing of the red crane’s boom sections would take place on the left side of the yellow crane. As a result, the counterweights would always be on the right side of the yellow crane, where no employees would be working. Therefore, it was determined that ropes only needed to be hung between the outriggers of the yellow crane on the left side that stated “DANGER—SWING AREA – RESTRICTED.” In fact, the CSHO only sees employees working on the left side of the yellow crane. However, the CSHO asked an employee to position the yellow crane so the counterweights are on the left side of the crane. Thinking nothing of it, the employee complied and allowed the CSHO to take pictures of the crane in that position.
OSHA cited the company with two instances of failing to adequately mark the hazardous area boundaries created by the swing radii of the yellow and red cranes’ rotating superstructures in violation of the crane standard at 29 C.F.R. § 1926.1424(a)(2)(ii).
The company contested the citations, claiming, in part, there were no employees exposed to the swing radius of either crane. The judge agreed. As a direct result of the CSHO not taking quantitative measurements, the judge held the OSHA Secretary was unable to prove the red crane’s rotating superstructure, without counterweights, posed a reasonably foreseeable risk of striking the two employees standing at one end of the crawler. The judge also found the employees’ matter-of-fact recounting of the CSHO’s instruction to rotate the yellow crane more credible than the CSHO’s vague recollection. The judge stated that the only time the left side of the yellow crane became a zone of danger was when the employee rotated the counterweights to that side after the CSHO instructed him to do so. Based on the work plan, the judge further stated it was not reasonably foreseeable (or predictable) that an OSHA CSHO would instruct the operator of the yellow crane to swing the counterweights to the left side of the crane so he could document the counterweights extended past the boundary marker on that side. Due to the lack of evidence, the judge found the Secretary also failed to show the rotating superstructure of the yellow crane posed a reasonably foreseeable risk of striking, pinching, or crushing an employee in an accessible area on the left side. Therefore, the judge ultimately vacated the citation.
Protecting Rights
OSHA may have the legal authority to inspect the workplace, but a company and its employees also have rights. It is important to balance both rights throughout the inspection process.
If OSHA does not witness a violation or otherwise has evidence of employee exposure to a violation, it cannot create or recreate exposure in photographs by asking an employer to stage the scene. If OSHA insists, contact an experienced OSHA attorney or upper management official for advice.
In NACR, the Secretary largely rested the case on the photographs and evidence obtained by the CSHO. Time and money may have been saved if the employees declined to move the equipment into the requested position. Even trained CSHOs do not always have the required expertise to understand some of the more complex OSHA standards, such as the crane and derrick standard, or how the equipment operates at the worksite, especially during different types of activities. As was the case in NACR, employers might be more knowledgeable than the CSHO in these areas and should stand behind their expertise and attempt to educate the CSHO about the operations.
Proposed Clarification of Crane and Derricks Standard
OSHA has proposed amendments to the Cranes and Derricks in Construction Standard. The suggested changes include revising wording relating to voltages (AC and DC), broadening exclusions for forklifts, correcting an error permitting body belts to be used as a personal fall arrest system (as opposed to a personal fall restrain system), removing ambiguity regarding crane verbiage, and correcting other errors found in the current standard. These amendments likely will not change the application of the standard significantly, but they would help clarify and correct mistakes.
Author: Melanie L. Paul & Kristina T. Brooks
You might also like
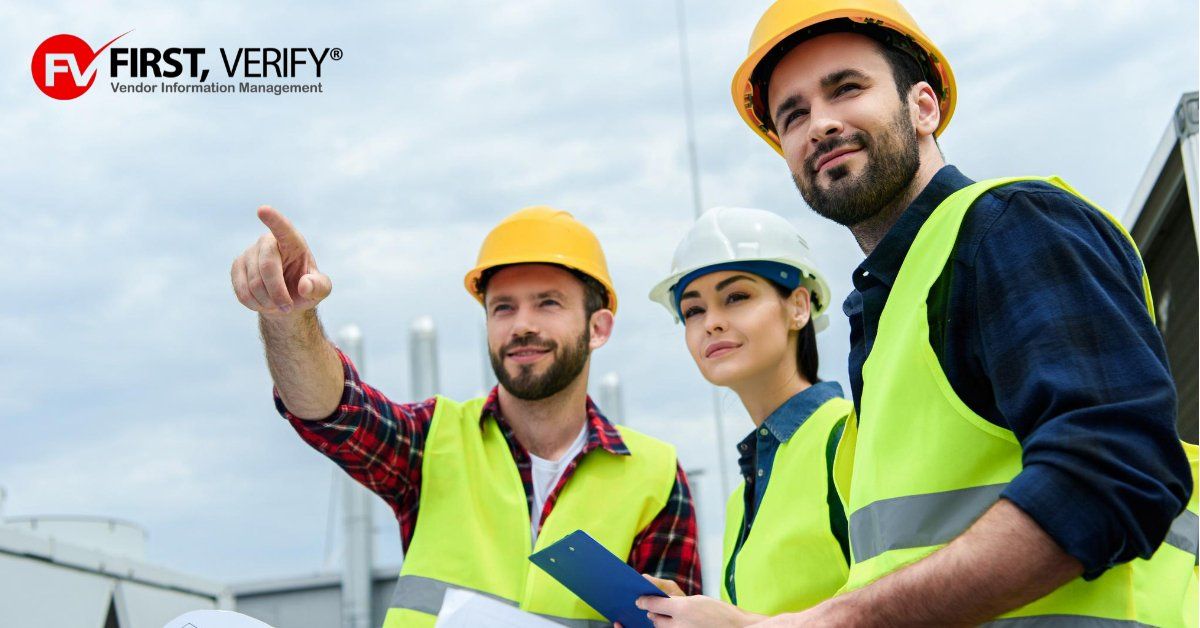