Is Behavior-Based Safety Training Right for Your Organization?
For example, for organizations that operate in construction, you might develop a BBS checklist focused on common contractor and worker issues, such as use of heavy equipment, or as simple as hammering a nail. Checklists often include the basics of the observation (time, date, location, behaviors observed, observer) and the number of safe and unsafe observations of the reviewer. The checklist also includes fields for any feedback and comments provided to the employee.
Critics of BBS say that it imposes unrealistic requirements for gathering data, which can result in what’s commonly known as “garbage in… garbage out.” And with suspect data, organizations could end up blaming and punishing workers if idealistic expectations fail. With that said, a counterargument is that proper design and management area given for the success of any program.
How to Develop a BBS Program
When you look at the at-risk data and are deciding what types of solutions or interventions to make, always consider each of these three components.
- Safety management system - how does the current system that is being used to manage safety in the workplace need to be changed to increase the amount of “safe behavior”?
- Once you have defined in observable terms - remember we can “see” behavior - you next need to look at the design of a process for collecting data on how frequently “at-risk” or “safe” behavior is occurring.
- Design of the process should be done in a team approach - Involve selected representatives of the hourly work force, union, management and safety staff. Everyone needs to feel comfortable with the process that is designed and what their various roles and responsibilities will be.
Some amount of redesign of the work zones or engineering controls could be put in place to reduce or eliminate some of the safety risk behaviors that get observed.
The intent is to increase safe behavior awareness. What sort of self-monitoring techniques can be employed? How can the necessary behavior changes be shaped and reinforced?
An effective solution may often require a combination of all three approaches, which is then used to design the safety orientation training that will work best in conjunction with the findings of the BBS components.
You might also like
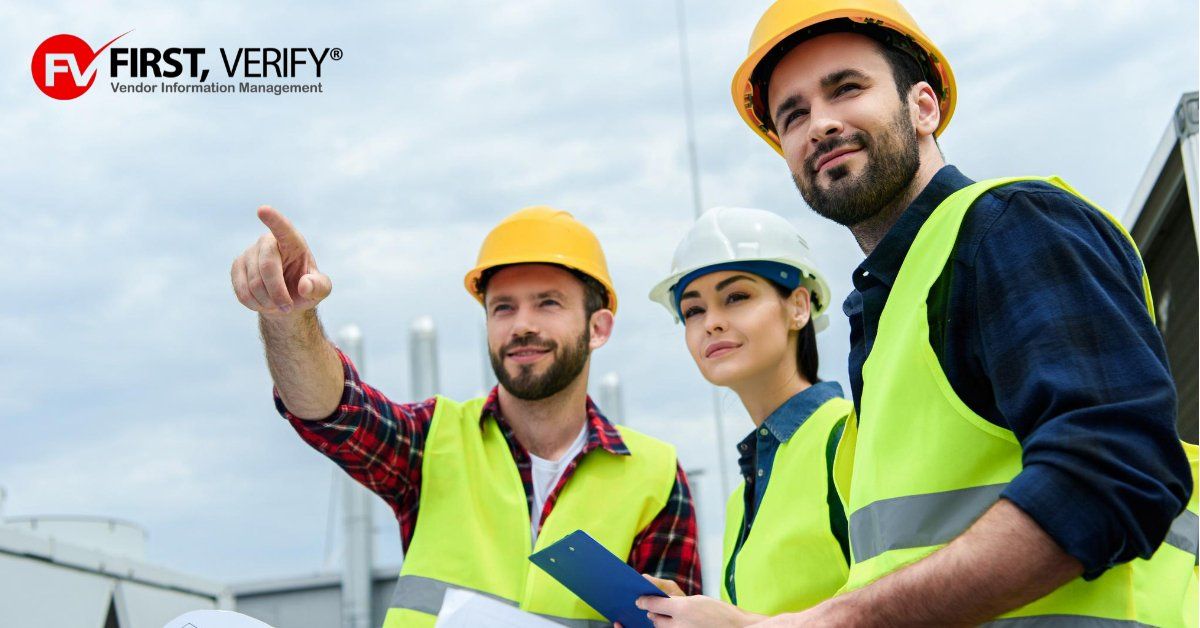